Sintering Behavior of the β″-alumina Solid Electrolyte for Battery Applications
A. Niyompan, K. Srisurat, R. Tipakonthitikul, K. Pengpat and T. Tunkasiri
The β″-alumina solid electrolyte proposed for the application in the electric vehicle battery system was prepared via a liquid phase sintering method. The main aim of the study is to reduce sintering temperature which is normally required as high as 1700°C. The MgO-stabilized Naβ″-alumina with the composition Na1-xMg2xAl5-xO8 where x = 0.125 was prepared. The mixture of Na2CO3, MgO and γ -Al2O3 were produced and well-mixed by wet ball milling method. Then, calcination was performed at 1200°C for 10 h. Calcined β″-alumina was then added with a sintering aid, CuO, at several concentrations prior to forming by a dry pressing technique. The green pellets were then sintered at different temperatures with constant dwell time for 4 h. Phase identification on calcined powders indicate that β″-alumina present as a mojor phase co-existed with tiny proportion of β′-alumina. Co-existence of these two phases is commonly found for this particular system. Phase checking for sintered samples with CuO additive show no phase change but concentration ratio of the β′-alumina seem to increase with increasing sintering temperature and mol% of the CuO. Sintering at 1550°C, the higher densification is clearly observed for ceramic with higher CuO content, i.e. 5 and 10 mol%. Layered-structure of the β″-alumina can be clearly seen from the SEM micrographs. The SEM results also show that higher CuO content promoted a higher grain development and produced less porosity. Dc conductivity values of the samples with CuO adding are reasonable high comparing to that of without CuO adding. This study has been show that β″-alumina produced by liquid phase sintering here is considerably appropriate to the application in the battery of electric vehicles.
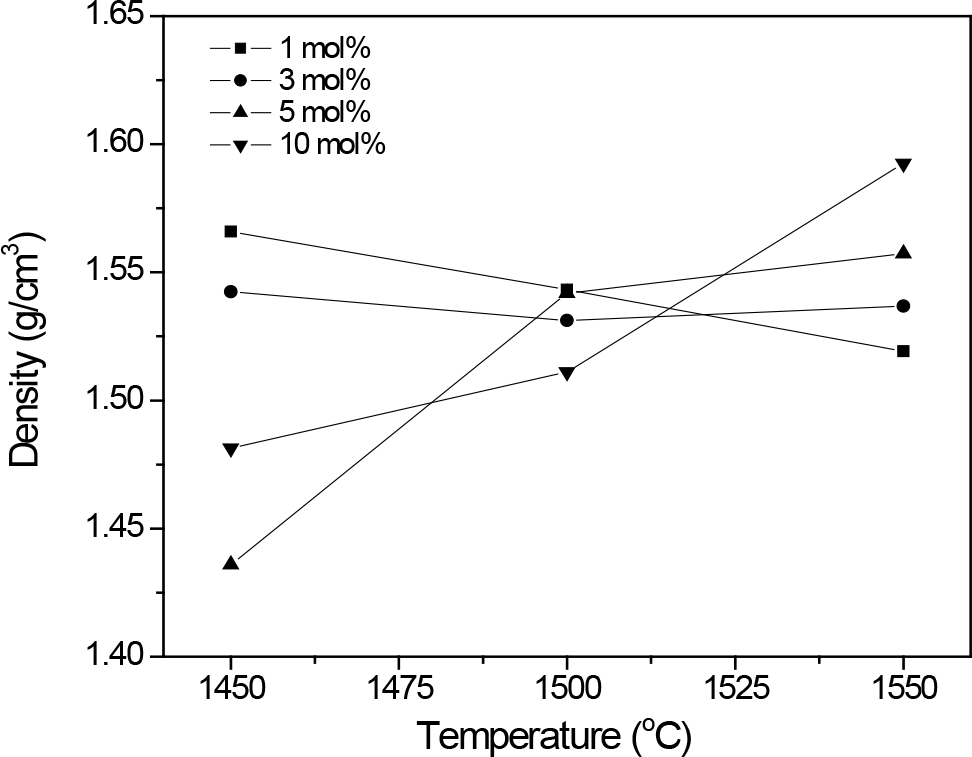
Introduction
Using β″-alumina solid electrolyte as the conductive layer in the electric car battery has been achieved and the product has been commercially named as ZEBRA battery [1, 2]. Generally, nominal composition of the β″-alumina is Na(1-x)Al5O8 (where 0 < x < 3) [3] but addition of MgO is required to stabilize the β″-alumina. Thus, the corresponding composition becomes Na1-xMg2xAl5-xO8 where x is essentially fixed at 0.175. However, dense MgO-stabilized β″-alumina prepared via conventional solid state sintering can be achieved with only at high sintering temperature i.e. 1700°C. At this high sintering level, loss of Na content may also takes place because of its volatile, leading to alteration of composition or sometime involving of the phase change. Such high temperature sintering is also uneconomical and requires a special instrumentation. Alternative methods have been also employed to overcome this problem such as sol-gel method [4] and microwave sintering [5-7] etc. But those methods require a complicate process as well as complex starting materials and yielding only a small quantity of the product.
In this work, attempt is to find the appropriate preparation route that be able to reduce the sintering temperature of the MgO-stabilized β″-alumina ceramic by employing a liquid phase sintering technique. Thus, sintering behavior of the MgO-stabilized β″-alumina with presence of the additive is investigated. CuO was selected as the sintering aid. The effect of CuO addition was studied in term of densification and microstructure arrangement. The effect on ionic conductivity was also determined.
Experimental
According to β″-alumina preparation, high purity reagent chemical, i.e. Na2CO3, MgO and synthetic γ-Al2O3 were used as starting materials. The γ-Al2O3 obtained in our laboratory from calcination of the AlO(OH) which was prepared by a precipitation method. A mixture of γ-Al2O3, Na2CO3 and MgO was produced according to a desired weighting and ball-milling with YZT balls media for 20 h. Then, calcination was performed at 1200°C for 10 h with heating rate and cooling rate of 5 °C/min. The calcined powder was then subjected to phase identification using XRD technique. Addition of CuO in varying proportion, i.e. 1, 3, 5 and 10 mol%, were applied tCalcined powder prior to green ceramic pellets formation via dry pressing technique. The pellets were then sintered at temperature range 1450-1550°C for 4 h and phase identification was carried out again. The morphology of β″-alumina powder and β″-alumina ceramics were analyzed by Scanning Electron Microscopy (SEM). The densities of sintered pellets were determined using Archimedes principle by weighting in air and distillate water at room temperature. Finally, dc ionic conductivities of the ceramic samples were determined using LCR meter.
Results and Discussion
Fig. 1 presents the XRD pattern of the calcined powder which β″-alumina can be identified as a major product. The pattern of β′-alumina is also visible but with only small proportion. Co-existence of these two phases seemed to be a common product obtained from this particular system because they have only slightly different oxygen stacking sequence [8].
Figure 1. XRD powder pattern of the calcined β″-alumina.
Figure 2. XRD powder patterns of β″- alumina ceramics sintered at 1450℃ with variation of CuContent.
The XRD powder patterns of sintered samples for various CuContents and three different sintering temperatures are shown in Fig. 2-4. In Fig. 2, the bulk ceramics show nChange in phase type, presence of β″-Al2O3 still be observed as well as an impurity β′-Al2O3. Increasing of CuConcentrations did not induce any change in the relative intensities of both phases. Rising sintering temperature to 1500℃ also gives insignificant change in phase relationship as we can observe similar profile comparing between powder patterns in Fig. 2 and Fig. 3. However, as the sintering temperature rise to 1550℃, diffraction peaks belonged to α -Al2O3 are starting to visible in the patterns of β″-Al2O3 ceramics contained a higher CuContent (Fig. 4). Relative intensity progress of peaks belonged to β′-Al2O3 can be also observed. These results indicate that phase transformation took place for higher sintering temperature and higher CuContent. Some proportions of β″-Al2O3 might transform to β′-Al2O3 and partially decomposed to give α -Al2O3. This observation is not surprise because β″-β′ transition is readily occurred at high temperature as suggested by Näfe et al. [9]. There might be also a significant loss of Na content in the samples sintered at this temperature which induced chemical composition alteration and phase transformation. Occurrence of the α -Al2O3 phase may be associated to involvement of CuContent as its diffraction peaks are noticeable for sample with 5 and 10 mol% of CuO.
Figure 3. XRD powder patterns of β″-alumina ceramics sintered at 1500℃ with variation of CuContent.
Figure 4. XRD powder patterns of β″-alumina ceramics sintered at 1550℃ with variation of CuContent.
Figure 5. Apparent densities of β″-Al2O3 ceramic samples sintered at different temperatures and added with different CuConcentration.
Table 1. Ionic conductivity (σ dc) measured at 300℃ of the β″-Al2O3 ceramics sintered at different temperatures.
The measured apparent density values of sintered samples shown in Fig. 5 reveals effect of CuO on sinterability of the β″-Al2O3 ceramic as increasing of densities with increasing sintering temperature are only observed for ceramic that contained higher CuO, i.e. 5 and 10 mol%. At lower CuConcentration, there is no pronounced effect from CuO to densification of the β″-Al2O3.
Fig. 6 shows the represent SEM micrographs of the β″-Al2O3 ceramics sintered at 1450℃. The β″- Al2O3 particles were seen as packing of several platelets. Plate thickness and size were developed with CuContent. Increasing CuConcentration also improved densification as less porosity is observed. However, determined density values for these samples set do not show the same trend as the observed microstructure. It may be probably due to formation of β″-Al2O3 platelets cluster or the effect of inhomogeneity distribution of CuContent which then affect the overall bulk density.
Table 1 reports the ionic conductivities measured at 300℃. Basically, in creasing sintering temperature should give samples with higher ionic conductivity but this is seemed not tCertain for each group of the samples with the same CuContent. However, at the same sintering temperature, effect of CuConcentration can be distinguished, as the higher CuConcentration gives a lower ionic conductivity. This is not surprise because CuO impurities are play a role as blocking for Na+ migration. Fluctuation of ionic conductivity found in this work is mainly the consequence of microstructure arrangement. The same effect was also reflected by density values.
Figure 6. SEM micrographs of β″-Al2O3 ceramics sintered at 1450℃ with different CuContent: (a) 1 mol% (b) 3 mol% (c) 5 mol% and (d) 10 mol%.
Summary
Higher sinterability of β″-Al2O3 ceramics in temperature range 1450-1550℃ can be promoted by introduction of the sintering aid, CuO. Involvment of CuO for its higher content and at higher sintering temperature also induced phase change. The change was also thought to originated from loss of Na+ . Dc ionic conductivity values measured at 300℃ revealed a strong effect of microstructure and density of the ceramics on the Na+ mobility.