Influence of Adding High Purity Alumina in Electrolyte on Performance of Lithium-ion Batteries
LIU Lin, ZHANG Shumiao, GAO Hong
The electrochemical performance of lithium-ion batteries can be effectively improved by adding a small amount of additives into the electrolyte. In this study, nano Al2O3 powder was used as the additive of lithium-ion battery electrolyte, the influence of the amount of nano Al2O3 on the electrochemical properties of lithium-ion batteries were studied by galvanostatic testing and electrochemical impedance spectroscopy. The experimental results showed that the addition of nano Al2O3 in the electrolyte could improve the conductivity of the electrolyte, reduce the charge transfer resistance, and improve the electrochemical performance of lithium-ion batteries. When the addition amount of nano Al2O3 was 1. 0%, the lithium-ion battery had the minimum polarization in the charging and discharging process, and the discharge specific capacity reached the peak 155.4mAhg-1 . Moreover, its discharge capacity was 147.5mAhg-1 over 50 cycles with a capacity retention rate of 94. 9% at a rate of 0. 1 C.
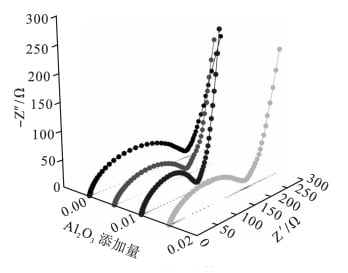
Introduction
Lithium-ion batteries have many advantages, such as high discharge platform, small self-discharge, small volume, light weight, high specific capacity, no memory effect, little pollution, long cycle life, etc. [1-2], so they have become the development focus of secondary batteries. Lithium-ion batteries generally contain three parts: positive material, negative material and electrolyte. Electrolyte plays the role of ionic conduction and electronic insulation between the positive and negative electrode of lithium-ion battery, which is known as the “blood” of lithium-ion battery. The electrolyte of lithium-ion battery is usually composed of organic solvent and soluble lithium salt. Lithium electrolyte salt can provide enough lithium ions to ensure that lithium ions are removed/embedded between the positive and negative electrodes during the charging and discharging cycle, thus completing the battery’s charging and discharging cycle. The properties of electrolytes have important effects on the battery’s cycle life, operating temperature range, charge-discharge efficiency, safety and power density. Commonly used lithium electrolytes include lithium hexafluorophosphate (LiPF6), lithium hexafluorborate (LiBF4), lithium perchlorate (LiClO4), lithium hexafluorararsenate (LiAsF6) and lithium diborate (LiBOB) [3-4]. Common solvents for electrolyte solutions include vinyl carbonate (EC), dimethyl carbonate (DMC), diethyl carbonate (DEC) and ethyl carbonate (EMC) [5-6].
The performance of Li-ion battery is largely affected by the properties of electrolyte, and the electrolyte of different systems is used in Li-ion battery with different functions. Adding a certain amount of non-energy storing substances to the electrolyte can improve the conductivity of the electrolyte, the charge-discharge performance, discharge efficiency, service life and safety performance of the battery. These non-energy storing substances are called additives [7]. According to its mechanism of action, additives can be divided into conductive additives, flame retardant additives, overcharge protection additives, low-temperature resistance additives, thermal stability enhancement additives, acid and water content control additives, etc. [5, 8-9].
The organic electrolyte will absorb water in the air, and the electrolyte will contain trace impurity hydrofluoric acid (HF). When the content of both is too high, LiPF6 decomposition will be caused, and the solid electrolyte interface film (SEI film) will be damaged [10]. When oxides such as alumina and magnesium oxide and carbonate of lithium or calcium are added to the electrolyte as additives, the additives can react with trace HF in the electrolyte, thus reducing the HF content, reducing the reaction between HF and the active substance on the electrode and the decomposition of LiPF6, thus improving the stability of the electrolyte and improving the performance of the lithium-ion battery [11]. In this paper, DEC, DMC and EMC were used as solvents [12], and LiPF6 was used as solute to prepare electrolyte. Different amounts of nano-alumina were added into the electrolyte to study the influence of the addition amount of nano-alumina on the electrochemical performance of lithium-ion batteries.
1 Experimental Part
1.1 Main raw materials and equipment for experiment
Nano-alumina (Al2O3), 99.99%; Lithium iron phosphate (LiFePO4); Acetylene black (C), polyvinylidene fluoride (PVDF), battery shell; N-methylpyrrolidone (C5H9NO); Ethylene carbonate (EC), dimethyl carbonate (DMC), ethyl carbonate (EMC), lithium hexafluorophosphate (LiPF6).
CT-3008W-5V constant current charge-discharge tester; Button type battery slicer, button type battery sealer; CHI660E electrochemical workstation.
1.2 Experimental Methods
1.2.1 Electrolyte preparation
DEC, DMC and EMC were mixed into a 25mm×25mm weighing bottle according to the volume ratio of 1∶1∶1, and 0.7596 g LiPF6 was added into the weighing bottle to prepare the basic electrolyte with molar concentration of 1mol/L. The additive nano-al2o3 with mass fraction of 0%, 0.5%, 1.0% and 1.5% was added into the basic electrolyte, and the final electrolyte was obtained by magnetic stirring for 5h.
1.2.2 Buckle battery assembly
Will be active substances LiFePO4, acetylene black, poly (vinylidene fluoride) (PVDF) according to the quality ratio of 8:1:1 grinding mixture, add N methyl pyrrolidone slurry system, apply evenly on the aluminum foil, and then in the 100 ° C in the vacuum drying oven drying 10 h; Put the dried positive electrode piece into the glove box after pressing, punching and weighing. In the argon atmosphere in the glove box according to the positive battery shell, electrode, electrolyte, diaphragm, lithium plate, relay, spring plate, negative battery shell assembly sequence; The assembled button battery was sealed with a sealer, and then tested after standing for 12h.
1.3 Experimental characterization methods
1.3.1 Charge-Discharge test Charge-discharge test is an important test method to analyze the electrochemical performance of electrode materials. At room temperature, the button battery assembled by adding different amounts of alumina electrolyte was tested by constant current charge-discharge tester. The charging cut-off voltage was 4.2V, the discharge termination voltage was 2.5V, and the charge-discharge ratio was 0.1C (170mAh·g-1).
1.3.2 AC impedance test
Ac impedance, also known as electrochemical impedance spectroscopy (EIS), is an electrochemical measurement method using a small amplitude sine wave potential (or current) as a disturbance signal. Because the small amplitude of the electrical signal to the system disturbance, on the one hand can avoid a large impact on the system; On the other hand, the relationship between the disturbance and the response of the system is approximately linear, which makes the mathematical processing of the measurement results easy.
In this experiment, the AC impedance test was carried out by clamping the marked button battery on the CHI660D electrochemical workstation with the corresponding clip, and the frequency range of the test was 10-2 ~ 106Hz. The properties of cathode materials are judged by the change of electrode potential.
2 Results and discussion
2.1 Influence of nano-al2o3 with different contents on charge-discharge performance In order to accurately detect the charge-discharge performance of the materials, the obtained samples were assembled into buckle batteries for detection. FIG. 1 shows the initial charging-discharge curve of LiFePO4 / Li battery samples assembled with nano-al2o3 of different contents at 0.1C rate.
FIG. 1 Initial charge-discharge curve from
FIG. 1 clearly shows that the discharge specific capacity of LiFePO4 / Li half battery at room temperature is 147.6mAh ·g-1, and the discharge specific capacity of electrolyte with different percentage contents of nano-al2o3 is similar, and the LiFePO4 / Li battery with 1.0% nano-al2o3 has the maximum discharge specific capacity. Its initial discharge capacity is 155.4 mAh·g-1. The initial discharge capacity of LiFePO4 / Li battery is 147.6 mAh·g-1, 153.2 mAh·g-1 and 149.7 mAh·g-1, respectively, when the nano-al2o3 content is 0%, 0.5% and 1.5%.
FIG. 2 shows the initial charg-discharge voltage platform curve of LiFePO4 / Li battery samples assembled with nano-al2o3 of different contents at 0.1C rate.
FIG. 2 Voltage platform curve of charge and discharge
As can be seen from FIG. 2, the potential difference between charging and discharging voltage platforms of LiFePO4 / Li battery samples assembled when the addition amount of nano-al2o3 is 0%, 0.5%, 1.0% and 1.5% is 102.9mV, 64.9mV, 55.2mV and 87.3mV, respectively. When the addition amount of nano-al2o3 is 1.0%, The minimum potential difference between the charging and discharging voltage platforms indicates that the polarization of LiFePO4 / Li lithium-ion battery assembled when the Al2O3 content is 1.0% is the minimum during the charging and discharging process.
FIG. 3 shows the cycle curve of charging and discharging of LiFePO4 / Li battery samples with different contents of nano-al2o3 at 0.1C rate.
Table 1 Discharge specific capacity and retention rate
As can be seen from Table 1, with the increase of nano-al2o3 addition, the discharge specific capacity and its retention first increase and then decrease. The reason is that when a certain amount of nano-al2o3 is added to the electrolyte, nano-al2o3 in the electrolyte can react with H2O and HF in the electrolyte to reduce the H2O and HF content in the electrolyte. The reaction between HF and the active substance of the electrode and the decomposition of LiPF6 can be reduced to improve the stability of the electrolyte, thus increasing the cycle life of the lithium-ion battery [13] and improving the charge-discharge cycle performance of the battery. However, when the amount of nano-al2o3 is too much, the nano-al2o3 will hinder the diffusion of lithium ions in the electrolyte, which is not conducive to improving the charge-discharge performance of lithium-ion batteries.
2.2 Influence of nano-al2o3 with different contents on AC impedance
FIG. 4 shows the AC impedance spectrum of LiFePO4 / Li lithium ion battery samples assembled with different nano-al2o3 addition amounts. In the figure, the horizontal coordinate (Z ‘) is the real part of the impedance, and the vertical coordinate (Z “) is the imaginary part of the impedance.
FIG. 4 AC impedance spectrum
As can be seen from FIG. 4, the AC impedance spectra of the four samples (as shown in Table 1) are composed of a slant line in the low frequency region and a semi-circle in the high frequency region [14]. The two regions respectively correspond to the transfer process of charge between the interface of LiF6PO4 electrolyte and the diffusion process of lithium ion in LiFePO4 in the electrochemical reaction [15]. The charge transfer impedance RCTS of LiFePO4 / Li cell samples assembled with 0%, 0.5%, 1.0% and 1.5% nano-al2o3 were 280Ω, 200Ω, 160Ω and 230Ω, respectively. The charge transfer impedance of the sample without nano-al2o3 in the electrolyte is larger than that with nano-al2o3, indicating that adding a certain amount of nano-al2o3 in the electrolyte can reduce the resistance of the electrolyte. However, with the increase of nano-al2o3 addition, the charge transfer impedance decreases first and then increases.
In conclusion, the electrochemical performance of LiFePO4 / Li battery samples is the best among all samples when the addition amount of nano-al2o3 is 1.0%.
3 Conclusion
With DEC, DMC and EMC as solvents and concentration of 1mol/L LiPF6 electrolytic liquid system, adding a certain amount of nano-al2o3 powder can improve the charge-discharge performance and cycle performance of lithium battery, reduce the battery impedance and improve the electrochemical performance of the battery. When the mass fraction of nano-al2o3 powder is 1.0%, the assembled LiFePO4 / Li battery has the best electrochemical performance.