Improvements of Conductivity and Multiplier Properties of Alumina Coated Cathode Material Na3V2-xMx(PO4)3 for Sodium-ion Batteries
A Invention Relates to A Preparation Method of Alumina Coated Cathode Material for Sodium-ion Batteries
The method doping rare earth metal in the cathode material, the band gap of the formed rare earth metal element -0 is smaller than that of V-0, which makes it easier for electrons to be excited from the valence band to the conduction band, and is conducive to promoting electron conduction. The coating material forms a solid melt with the contact agent, which is easy to be evenly coated, and the coating layer is not easy to fall off after firing. The method not only shorts the production cycle, but also ensures the uniformity of the coating, so that the coating material can also pass high temperature to form an ideal glass state coating, and improves the performance of the material.
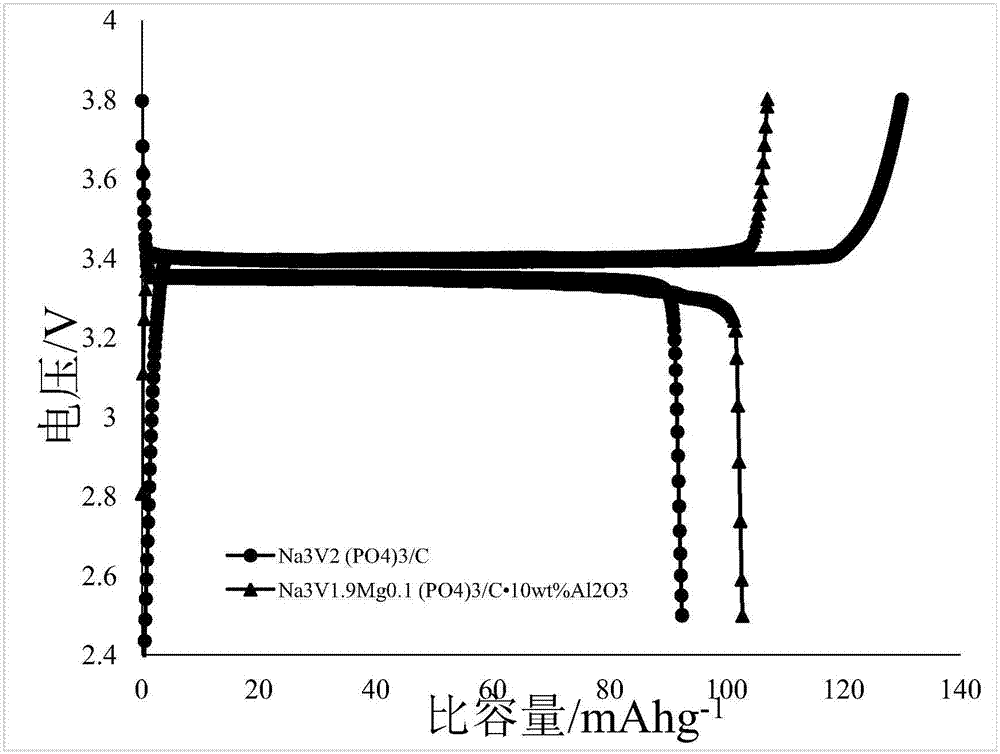
Technical field
The invention relates to the field of battery materials, in particular to a preparation method of alumina coated sodium ion battery cathode material.
Technical background
With the rapid development of society, the problems of energy and environment become more and more prominent, and it becomes more urgent to find new clean energy to replace oil resources. As a new type of clean energy, power battery has been paid more and more attention all over the world. Power battery is the core component of mobile electric appliances such as electric vehicle and electric tool. Pure electric vehicle (EV) or hybrid electric vehicle (HEV) with power battery as the main or auxiliary power source is one of the main development directions of the automobile industry.
Whether the manufacturing cost and energy consumption of batteries cause pollution to the environment and the recycling and utilization rate of resources will also become important indicators to evaluate battery materials. Battery development has the following significant characteristics: green battery development is rapid; Primary battery to secondary battery conversion, which is conducive to saving the earth’s limited resources, in line with the strategy of sustainable development; Batteries are becoming smaller, lighter and thinner. Sodium is one of the more abundant elements on Earth and has similar chemical properties to lithium, so it may also be suitable for lithium-ion battery systems. Compared with lithium-ion battery, sodium-ion battery has many advantages, such as low cost and good safety. With the deepening of research, sodium-ion battery will be more and more cost-effective, and is expected to replace lithium-ion battery in the future and be widely used. Moreover, in sodium-ion batteries, Al and N are not alloyed, so the negative collector fluid can choose to use Al foil, which can further reduce the price.
However, because the radius of sodium ion is larger than that of lithium ion, its energy density and power density are lower than that of lithium ion battery. However, the energy density of battery is not too high in the application of scale energy storage, and its cost and life are the focus of concern. Viewed from this perspective, sodium-ion batteries have a larger market competitive advantage over lithium-ion batteries in large-scale energy storage applications. The cathode material of sodium ion battery has poor conductivity, and the radius of sodium ion is larger than that of lithium ion, so it is more difficult to decant sodium than lithium, resulting in lower actual discharge capacity and poor multiplier performance. To solve this problem, researchers mainly use the method of cladding to improve its performance.
The traditional coating process is mainly liquid phase coating, that is, after the cathode material is fired, the liquid phase coating material is used for coating, and then drying or simple refiring to stabilize the coating on the surface of the material. The disadvantages of this kind of process are obvious: first of all, most of the coating materials are difficult to form liquid phase, that is, there are fewer coatings to choose from in this method; Secondly, in the process of firing after liquid coating, it is easy to destroy the coating layer, resulting in defects in the coating. Third, the coating process affects the properties of materials; Fourth, the overall process cycle is long and the production efficiency is low.
The invention content
The invention provides a preparation method for aluminum oxide coated anode material of sodium ion battery. The method doping rare earth metal into the cathode material, the band gap of the formed rare earth metal element-0 is smaller than that of V-0, which makes it easier for electrons to be excited from valence band to conduction band, and is conducive to promoting electron conduction. The coating material forms a solid melt with the contact agent, which is easy to be evenly coated, and the coating layer is not easy to fall off after firing. The method not only shorts the production cycle, but also ensures the uniformity of the coating, so that the coating material can also pass high temperature to form an ideal glass state coating, and improves the performance of the material.
To achieve the above purpose, the invention provides a preparation method for alumina coated anode material of sodium ion battery, which comprises the following steps:1. A method for preparing alumina coated anode material for sodium ion batteries, including the following steps:
(1) The cathode material doped with rare earth metal was prepared
The rare-earth metal-doped positive material group is Na3V2-xHox(PO4)3, where x=0.01-0.03;
According to the molar ratio of 3:(2-x):x:3 weighing sodium chloride, vanadium pentoxide, holmium nitrate and potassium phosphate;
The vanadium pentoxide, holmium nitrate and glucose were dissolved in deionized water and heated and stirred at 60-80 degrees to form a uniform mixed solution.
Add the sodium chloride and potassium phosphate to the above mixed solution and spin steam 3-4 at a vacuum temperature of 70-90℃;
The electrode material precursor was formed by vacuum drying at 100-150℃ for 5-20h. The electrode material Na3V2-xMx(PO4)3 was obtained by pre-sintering at 400-600℃ for 3-5h and high temperature sintering at 700-800℃ for 10-15h under nitrogen atmosphere. After cooling, the cathode material Na3V2-XMX (PO4)3 was obtained.
(2) Pretreatment of coating materials
The coating material is alumina, the particle size distribution D50 is less than 5μm, using boric acid as the contact agent, the boric acid and oxide according to the weight ratio of 1:(3-4) mixed, pulverized in high speed crusher for 15-20 seconds, so that its surface activation, fluffy state;
(3) Composite cladding
The rare-earth metal doped positive electrode material Na3V2-xMx(PO4)3 and the pretreated coating material are evenly mixed in the mixer according to the mass ratio (85-60):1;
Under atmospheric conditions, the mixed material is fired, the temperature rises to 860℃-950℃, heat preservation 10-15h, after cooling products.
Preferably, where in step (1) the amount of glucose added is greater than the amount by which it completely reduces V5+ to V3+ : the solute to solvent ratio in the mixed solution is 1:(5-10).
The invention has the following advantages and remarkable effects:
(1) The invention doping rare earth metal into the cathode material, the band gap of the rare earth metal element -0 is smaller than that of V-0, which makes it easier for electrons to be excited from the valence band to the conduction band, and is conducive to promoting electron conduction.
(2) the invention cladding materials and contact agent form solid solution, easy to uniform coating, and combine closely after firing, cladding layer is not easy to fall off, this method not only shorten the production cycle, and to ensure the uniformity of coating, can also make the cladding material through high temperature to form ideal coated glass state, improve the performance of the material.
Specific mode of implementation
Example 1
The rare-earth metal-doped positive material group is Na3V1.99Ho0.01(PO4)3; Sodium chloride, vanadium pentoxide, holmium nitrate and potassium phosphate were weighed according to the molar ratio of 3:1.99:0.01:3.
Dissolve the above vanadium pentahydrate, holmium nitrate and glucose into deionized water, and heat and stir at a temperature of 60 degrees to form a uniform mixed solution: the amount of the glucose added is greater than the amount that will completely reduce V+ to V3+ : the solute to solvent ratio in the mixed solution is 1:5.
Add the sodium chloride and potassium phosphate to the above mixed solution and spin steam for 3h at a vacuum temperature of 70℃; After vacuum drying at 100℃ for 5h, the electrode material precursor was formed. In the nitrogen atmosphere, the electrode material was pre-sintered at 400℃ for 3h and at 700℃ for 10h. After cooling, the cathode material Na3Vo.99M0.01(PO4)3 doped with rare earth metal was obtained.
The coating material is alumina, and its particle size distribution D50 is less than 5m. Boric acid is used as the contact agent, the boric acid and oxide are mixed according to the weight ratio of 1:3, and crushed for 15 seconds in the high-speed crusher, so that the surface is activated and the state is fluffed, and the pretreatment of the coating material is obtained.
The rare-earth metal doped cathode material Na3V2-xMx(PO4)3 and the pretreated coating material are evenly mixed in a mixer according to the mass ratio of 85:1; Under atmospheric conditions, the mixed material is fired, heated to 860℃, held for 10h, and the product is obtained after cooling.
Example 2
The rare-earth metal-doped positive material group is Na3V1.97Ho0.03(PO4)3, weighing sodium chloride, vanadium pentoxide, holmium nitrate and potassium phosphate according to the mole ratio of 3:1.97:0.03:3.
The vanadium pentoxide, holmium nitrate and glucose were dissolved in deionized water and heated and stirred at 80 degrees to form a uniform mixed solution. The amount of glucose added is greater than its total reduction of + to V3+ : the solute to solvent ratio in the mixed solution is 1:10.
Add the sodium chloride and potassium phosphate into the above mixed solution and spin steam for 4h at a vacuum temperature of 90℃; The electrode material precursor was formed by vacuum drying at 150℃ for 20h. The electrode material Na3V1.s7Ho0.03(PO4)3 was obtained by pre-sintering at 600℃ for 5h and high temperature sintering at 800℃ for 15h under nitrogen atmosphere. After cooling, the cathode material Na3V1.S7HO0.03 (PO4)3 was obtained.
The coating material is alumina, the particle size distribution D50 is less than 5μm, using boric acid as the contact agent, the boric acid and oxide according to the weight ratio of 1:4 mixed, crushed in the high-speed crusher for 20 seconds, the surface activation, the state of fluffy, obtained by the pretreatment of coating material pretreatment.
The rare-earth metal doped cathode material Na3V2-xMx(PO4)3 and the pretreated coating material are evenly mixed in a mixer according to the mass ratio of 60:1; Under atmospheric conditions, the mixed material is fired, heated to 950℃, held for 15h, and the product is obtained after cooling.
The product material of the above embodiment I and II was taken as the positive electrode, the sodium metal sheet as the negative electrode, the glass fiber membrane as the separator, the solute as 1M NaCl04, the mixture of solvent EC and DC (volume ratio 1:1), the additive as FEC with the mass fraction of 2% as the electrolyte, and the aluminum foil as the collector plate. Sodium ion batteries are assembled by stacking and pressing CR2016 buckle shell in the order of positive shell, fluid collector, positive electrode, electrolyte, diaphragm, electrolyte, negative electrode and negative shell. The first charge-discharge capacity is 164 and 166mAhg-1, respectively, and the capacity retention rate is above 99.2% at 10C rate for 150 cycles.