Effect of High Purity Alumina Coating on Polyethylene Diaphragm of Lithium Battery
ZHANG Rui-zhu, FENG Jia-he, LI Yan-yan, MA Shu-yun
To improve the safety performance of the battery diaphragm, polyethylene diaphragm is used as base membrane, polyacrylate and alumina are used as coating solution to develop one side high purity alumina coating diaphragm. Puncture strength of diaphragm is measured by CCY-02 puncture force tester, tensile strength of diaphragm is measured by XLWintelligent electronic tensile force tester, permeability of diaphragm is measured by TQD-G1 air permeability tester, liquid absorption rate of diaphragm is calculated by weighing; thermal shrinkage of diaphragm is detected by RSY-R1 thermal shrinkage tester at room temperature to study the mechanical properties, thermal stability, air permeability and moisture content of diaphragm by introducing coating layer. The microscopic characterization of the composite diaphragm was studied by FTIR, EDS, and SEM. After the high purity alumina coating was introduced, the comprehensive performance of the composite diaphragm is obviously improved: When the amount of polyacrylate in the coated solution is 6% and the amount of pure alumina is 40%, the overall performance of the diaphragm is optimal, puncture strength reached 785 g, transverse tensile strength of 158.6 MPa with the longitudinal tensile strength of 121.7 MPa, air permeability of 263 s/100 mL, the suction rate of 300%. Under vacuum at 130 ℃ for 1 h, the transverse thermal contraction is 2.18%, vertical collection shrink is 0.83%. The results of analysis the component and microscopic characterization of the composite diaphragm show that the surface of the modified membrane forms a well-distributed microporous structure, which promotes the transfer of lithium ions between positive and negative poles. Because of the physicochemical characteristics of alumina, the heat resistance of lithium battery diaphragm is improved. Therefore, the high purity alumina composite diaphragm plays a positive role. In general, the comprehensive performance of lithium ion battery diaphragm is greatly improved after the introduction of high purity alumina coating.
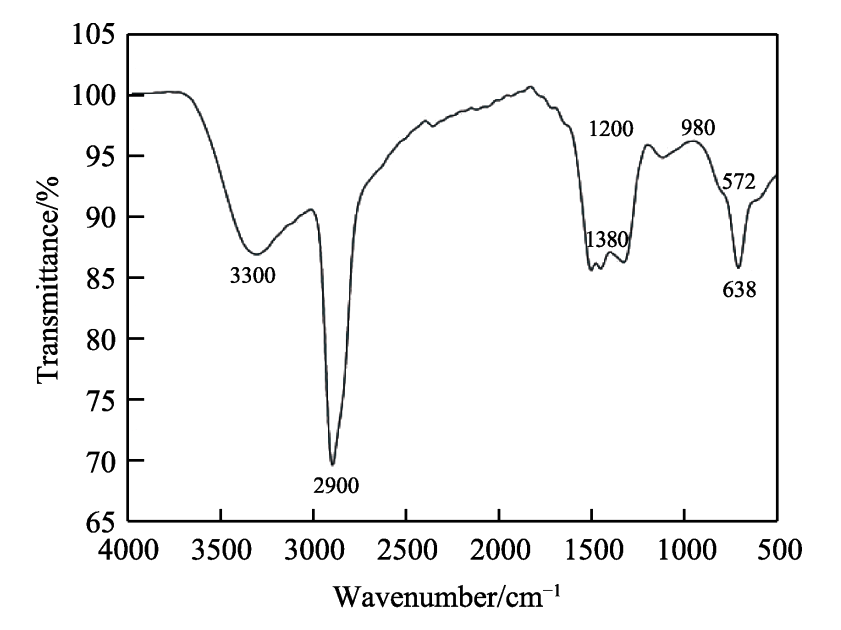
Introduction
With the rapid development of science and technology, batteries are more widely used in many industries. Lithium-ion batteries have been successfully used in mobile phones, computers and other electronic devices because of their many advantages, such as long cycle life, large energy density and high operating voltage [1]. In response to the national call for energy conservation and emission reduction, green electric vehicles have gradually had a large market, further promoting the development of lithium-ion batteries, but the requirements for lithium electronic battery related materials will be more stringent. Considering that to practice green development, it is imperative to expand the market demand for new energy vehicles, which will require lithium-ion batteries to have higher performance [2-4]. The components of lithium-ion batteries mainly include positive and negative electrodes, membranes and electrolytes. The diaphragm separates the positive and negative poles to prevent contact between the two poles and ensure that there is no short circuit inside the battery. At the same time, lithium ions can move freely between the positive and negative poles to prevent electrons from passing through [5-6]. The size of the battery capacity, the safety of use and the length of life are largely determined by the performance of the diaphragm [7-9]. Lithium-ion batteries generate a lot of heat during charging and discharging. In order to ensure the safety of batteries at high temperatures, the diaphragm must have excellent high temperature resistance [10-11]. Therefore, it is necessary to optimize and upgrade the lithium-ion battery separator. Xue et al. [12] developed a multifunctional coating for battery separators. The results show that the coating inhibits the formation of Li2S insulation layer and enables the sulfur cathode to be charged and discharged very fast. In addition, the coating has a strong adsorption force, which can prevent the polysulfide lithium from moving to the negative side of the lithium electrode, thereby improving the cycle life of the positive sulfur electrode. Cheng et al. [13] prepared a porous carbon nanosheet composite material and used it to modify the battery diaphragm. The results show that the modified cell membrane can not only block the movement of polysulfide, but also act as an electrocatalyst to catalyze the conversion of the intercepted polysulfide. Huang et al. [14] prepared a composite nanofiber membrane with high porosity and high tensile strength, which is expected to be used in high-performance lithium-ion batteries. It can be seen that in order to meet the application of diaphragm in high-performance batteries, one of the effective ways to modify the diaphragm is to introduce a coating layer.
At present, the diaphragm matrix of lithium-ion batteries is mainly polyethylene and polypropylene, but the melting point of polyolefin is relatively low, polyethylene melts at 128~135 ° C, and the melting temperature of polypropylene is 150~160 ° C, the battery will locally release heat during high-power charging and discharging, and when the temperature rises to 120 ° C, the diaphragm will appear closed-cell phenomenon; At 150 ° C, the diaphragm melts, the positive and negative electrodes contact, and the battery appears thermal runaway, which causes the battery to explode. Therefore, better performance diaphragms are needed to improve the safety of lithium batteries [15-18]. Polyethylene prepared by wet method is a common material in diaphragm. In this paper, polyethylene-based film is used as a adhesive, and a certain amount of high purity alumina is coated. The high purity alumina coating layer is prepared, and the related properties of composite diaphragm are tested. The high purity alumina coated composite diaphragm described in this paper has high puncture strength, tensile strength and liquid absorption rate, which is of great significance in ensuring the safety of high-performance lithium batteries.
1 Experiment
1.1 Experimental methods
1.1.1 Preparation of high purity alumina
Using imported high quality and high purity triboehmite as raw material, adding compound mineralizer, using special technology, after 1650℃ high temperature phase transformation, purified by depolymerization, flotation to produce high purity alumina, its purity reached 99.95%, iron mass concentration less than 100mg/L. The narrow particle size distribution of high purity alumina can reduce the plugging of the diaphragm, and the crystal morphology is spherical, which can not only promote the adhesion strength of the diaphragm matrix, but also meet the needs of different water-based slurry systems, and do not settle for a long time.
1.1.2 Preparation of polyethylene composite diaphragm
Using polyacrylate as adhesive and high purity alumina as inorganic reinforcing agent, the coating solution was prepared under the action of dispersant, thickener and wetting agent according to a certain proportion. The fine copper wire with clean surface is wrapped on the glass rod, and the coating liquid made by it is slowly and evenly coated on the polyethylene surface, and the composite diaphragm is obtained by vacuum drying at 70℃ for 6h.
1.1.3 Composite diaphragm performance test and microscopic characterization
1) Puncture strength test. The composite diaphragm was cut into a membrane with ϕ=100mm in diameter. The puncture strength of the diaphragm was measured at room temperature using a puncture force tester CCY-02. The test piece was fixed with a fixed clamp ring, and then at a speed of 50mm/min, the spherical steel needle r=0.5mm was used to Pierce the diaphragm, and the maximum load through the test piece was taken as the test result. Each group did 5 trials, and the average value was used as the final result.
2) Tensile strength test. The composite diaphragm was cut into 200mm×40mm splines, and the stretching rate was set to 25mm/min. The transverse and longitudinal tensile strength of the diaphragm were measured by tensile testing machine at room temperature. Each group was tested with 5 samples and the average was used as the final result.
3) Breathability test. The composite diaphragm is cut into a membrane with ϕ=50mm in diameter. The permeability of the diaphragm is measured by TQD-G1 permeability tester at room temperature. Adjust the measuring instrument to ensure a stable pressure difference (800Pa) on both sides of the sample, set the time to 1min, measure the gas flow through the unit area of the sample vertically, and calculate the air permeability. Each group tested 5 samples, and the average value was used as the final result.
4) Liquid absorption rate test. Cut the composite diaphragm into a sample of 30mm×30mm to be tested, dry under vacuum at 70℃ for 6h, and weigh as m0. Then soak the diaphragm fully with electrolyte for 2h, remove the diaphragm, remove excess electrolyte, and weigh again as m1. The calculation formula is shown in equation (1). Each group tested 5 samples, and the average value was used as the final result.
5) Heat shrink performance test. The composite diaphragm was cut into a sample of 100mm×100mm to be tested, and the heat shrinkage of the diaphragm was detected by RSY-R1 heat shrinkage tester at room temperature. The temperature was set at 130℃ and the holding time was 1h. 5 samples were selected for each measurement group, and the average value was taken as the final result.
6) Composition detection of composite diaphragm. The surface composition of composite diaphragm was detected by Fourier transform infrared spectrometer and X-ray energy spectrometer, and the surface of sample was cleaned with anhydrous ethanol before infrared spectrum detection. Before X-ray energy spectrum detection, the sample needs to be sprayed with gold by ion sputtering instrument.
7) Microscopic characterization. The composite diaphragm was microscopically characterized by EM-30 scanning electron microscopy. Before characterization, the sample was vacuum-dried at 60℃ for 2h, and then gold was sprayed on the diaphragm sample with an ion sputtering instrument, and the composite diaphragm was microscopically characterized.
2 Results and discussion
2.1 Influence of alumina content on diaphragm performance
The coating solution contains polyacrylate, alumina powder and other substances, and the content of these two substances has a great influence on the performance of the diaphragm. The previous experiments showed that when the content of polyacrylate was small, the adhesion between the coating and the base film was small. If the content is too much, it will cause the alumina powder to agglomerate, form large particles, and block the membrane pores. In summary, combined with the experimental data, the mass fraction of polyacrylate in the coating solution was initially selected as 6%, and the effect of alumina content on the diaphragm performance was studied.
2.1.1 Influence of alumina content on diaphragm puncture strength
As can be seen from Figure 1, the puncture strength of the composite diaphragm increases with the continuous increase of Al2O3 content, which not only improves the resistance of the diaphragm to penetration, effectively reduces the probability of positive and negative electrode contact, but also ensures the safety of the lithium battery to a certain extent. This is because Al2O3 in the coating layer has a high hardness, small particle size and uniform distribution of Al2O3, and its surface effect is significant, so it shows excellent plasticity and toughness, and enhances the impact resistance of the diaphragm [19]. However, the experiment found that when the content of Al2O3 is relatively small, its gain on the diaphragm performance is not large, if the content of Al2O3 is too high, when the mass fraction exceeds 40%, the alumina particle agglomeration tendency increases, although the puncture strength increases, but the other properties of the diaphragm will decrease.
Fig.1 Effect of Al2O3 content on puncture strength of diaphragm
2.1.2 Influence of alumina content on tensile strength of diaphragm
As can be seen from Figure 2, with the continuous increase of alumina, the transverse tensile strength of the diaphragm first increases and then decreases, reaching a maximum of 158.6MPa. The longitudinal tensile strength also increased first and then decreased, reaching a maximum of 121.7MPa. This is mainly because hydrogen bond is formed between polyacrylate and alumina under the action of secondary bonding force, and the diaphragm forms a network structure under the action of strong bonding force, which increases the cohesion of the diaphragm, so the tensile strength of the composite diaphragm is significantly improved [20-22]. Due to the increasing Al2O3 content, the agglomeration phenomenon is serious, the particle dispersion is uneven, which reduces the van der Waals force between molecules, resulting in a large number of stress concentration points, the membrane is stressed unevenly, and the tensile strength is also reduced.
Fig.2 Effect of Al2O3 content on tensile strength of diaphragm: a) transverse tensile strength; b) longitudinal tensile strength
2.1.3 Influence of alumina content on diaphragm permeability
As can be seen from Figure 3, with the continuous increase of Al2O3, the permeability of the diaphragm increases rapidly, and when the mass fraction of Al2O3 exceeds 40%, the permeability gradually decreases. This is mainly because Al2O3 particles uniformly attached on the surface of the diaphragm can not only improve the distribution of pore size, but also provide a larger specific surface area for the diaphragm, provide more active sites, and provide more holes for the electrolyte [23-24].
Fig.3 Effect of Al2O3 content on permeability of diaphragm
When the Al2O3 content continues to increase, more than 40%, it will lead to serious particle agglomeration phenomenon, large particles will block the aperture, so that the permeability of the diaphragm is reduced.
2.1.4 Influence of alumina content on liquid absorption rate of diaphragm
It can be seen from Table 1 that the addition of Al2O3 can improve the liquid absorption rate of the diaphragm, and the diaphragm has a certain amount of liquid absorption to ensure the transmission of lithium ions. When the mass fraction of Al2O3 increases from 0% to 20%, the liquid absorption rate of the diaphragm is greatly improved, mainly because the surface of Al2O3 contains a large number of hydrophilic hydroxides, which improves the wettability of the electrolyte to the diaphragm and thus increases the liquid absorption rate of the diaphragm [25-27]. When the Al2O3 mass fraction is increased from 20% to 40%, the liquid absorption rate of the diaphragm has increased, but the growth rate is slow. Continue to increase Al2O3, the content of polyacrylate in the coating liquid also gradually increased, and the high-viscosity polyacrylate will cover some Al2O3 particles, and change its surface properties, so that it loses its hydrophilic ability, thereby reducing the liquid absorption rate of the diaphragm.
Tab.1 Effect of Al2O3 content on suction rate of diaphragm
2.1.5 Influence of alumina content on thermal shrinkage performance of diaphragm
The shrinkage rate of the diaphragm is large, which will lead to thermal runaway under high temperature environment, affecting the normal use of the battery [28]. As can be seen from Table 2, under the conditions of test temperature of 130℃ and treatment time of 1h, both transverse and longitudinal thermal shrinkage of composite diaphragm decrease with the increase of Al2O3 content, which is because the viscous polyacrylate can make Al2O3 particles firmly adhere to the surface of the base film [29-30]. In addition, Al2O3 itself has a high melting point. It can effectively improve the heat resistance of the diaphragm, and the Al2O3 particles and polyacrylate can form a porous network structure, which can inhibit the deformation of the diaphragm, so the thermal shrinkage rate of the diaphragm is reduced. The shrinkage rate of the diaphragm is large, which will lead to thermal runaway under high temperature environment. When the temperature inside the battery continues to rise and reaches the melting point of polyethylene, the diaphragm will produce thermal closing effect [31], blocking the ion transfer between the positive and negative electrodes and ensuring the safety of the battery.
Tab.2 Effect of Al2O3 content on thermal shrink age of diaphragm
Considering the influence of Al2O3 content on diaphragm puncture strength, tensile strength, permeability, liquid absorption rate, thermal shrinkage, etc., the experiment determined that when the mass fraction of Al2O3 in the coating solution reached 40%, the comprehensive performance of the composite diaphragm reached the best, and the puncture strength value reached 770g. The transverse tensile strength and longitudinal tensile strength reached 158.6MPa and 121.7MPa respectively, the air permeability reached 263s/100mL, and the liquid absorption rate reached 300%. At the same time, the transverse thermal shrinkage of the diaphragm is 2.18%, and the longitudinal thermal shrinkage is 0.83%, while the lithium battery diaphragm industry stipulates that the thermal shrinkage of the diaphragm should be less than or equal to 6%, obviously, the composite diaphragm has good thermal shrinkage performance.
2.2 Influence of polyacrylate content on diaphragm performance
The adhesive used in the experiment is polyacrylate, and its content also has a certain influence on the related properties of the composite diaphragm. Combined with the experiment, the content of polyacrylate has a significant effect on the porosity and puncture strength of the diaphragm. The mass fraction of Al2O3 in the coating solution was 40%, and the influence of the mass fraction of polyacrylate in the coating solution (0%, 2%, 4%, 6%, 8%, 10%) on the membrane porosity and puncture strength was studied.
As can be seen from Table 3, polyacrylate can improve the viscosity of the coating solution, while the porosity of the diaphragm increases first and then decreases. The skeleton structure of polyacrylate can prevent adjacent particles from getting close to each other, thus reducing the van der Waals forces between particles, increasing the fluidity of the coating solution and improving its stability [32-33], and also promoting the uniform distribution of particles in the coating solution and improving the porosity of the diaphragm. When the mass fraction of polyacrylate exceeds 6%, due to its own viscosity, the viscosity of the coating solution increases rapidly, and Al2O3 particles are easy to accumulate in the pores of the polyethylene diaphragm, forming local dense areas [34], and the porosity of the diaphragm also decreases. However, the puncture strength of diaphragm increased with the increase of polyacrylate content. This is mainly because the polyacrylate has a stereostable effect, so that the Al2O3 particles are evenly dispersed [35]. In addition, polyacrylate can enhance the adhesion of the coating solution, improve the organization, so that the Al2O3 particles disperse and penetrate into the base film, forming a dense mesh structure, and improve the puncture strength of the diaphragm.
Tab.3 Effect of polyacrylate content on diaphragm properties
Considering the influence of the content of polyacrylate on the properties of the membrane, the experiment determined that the optimal addition of polyacrylate in the coating system was 6%, the porosity of the membrane was 46.1%, and the puncture strength was 792g.
2.3 Composition analysis of composite diaphragm
FIG. 4 shows the composition analysis diagram of the composite diaphragm. As can be seen from Figure 4a, the absorption peaks around 572cm-1 and 638cm-1 are characteristic peaks of alumina itself, indicating that alumina is well attached to the polyethylene diaphragm, thereby improving the relevant properties of the diaphragm. The absorption peak at 980cm−1 is the characteristic peak generated by H-C == C-H deformation vibration. The absorption peak at 1200cm−1 is the characteristic peak of C-O stretching vibration. The absorption peak at 1380cm−1 is the characteristic peak generated by -CH3 skeleton vibration. 2900, 3020 and 3300cm−1 are the characteristic peaks of the unique functional groups of olefin, where 2900cm−1 is the characteristic peak generated by the antisymmetric stretching vibration of -CH3, 3020cm−1 is the characteristic peak generated by the == c-h stretching vibration, and 3300cm−1 is the characteristic peak generated by the ≡ c-h stretching vibration. In addition, it can be seen more intuitively from the X-ray energy spectrum analysis that the composite diaphragm contains oxygen and aluminum elements, indicating that alumina is indeed attached to the polyethylene diaphragm.
Fig.4 Composition analysis of composite diaphragm: a) FTIR of composite diaphragm; b) EDS of composite diaphragm
2.4 Morphology and structure analysis
FIG. 5a shows the surface topography of polyethylene diaphragm. It can be seen that the membrane micropores are flat and “streamlined” and evenly distributed on the surface of the membrane, which can ensure the passage of ions, but the efficiency is low and the safety is poor. Figure 5b shows the surface topography of the composite diaphragm after being coated with high purity alumina. It can be seen that there are many micro-pores on the surface of the coated diaphragm, and the size and distribution of the pores are also relatively uniform. These micro-pores can ensure the efficient movement of lithium ions between the positive and negative electrodes. The battery diaphragm with excellent performance has a large internal aperture and a small surface aperture, so as to ensure that the battery diaphragm has a large liquid absorption volume, while the smaller surface aperture has a relatively large capillary force, thereby improving the liquid absorption and liquid retention ability of the diaphragm [36-37], and the diaphragm coated with high purity alumina composite has just this performance.
Fig.5 SEM of diaphragm: a) polyethylene diaphragm; b) composite diaphragm
3 Conclusions
1) When the mass fraction of polyacrylate in the coating solution is 6% and the mass fraction of high-purity alumina is 40%, the overall performance of the diaphragm reaches the best, the puncture strength value is 785g, the transverse tensile strength is 158.6MPa, the longitudinal tensile strength is 121.7MPa, the air permeability is 263s/100mL, and the liquid absorption rate is 300%. Under vacuum condition of 130℃ for 1h, the transverse thermal shrinkage is 2.18%, and the longitudinal thermal shrinkage is 0.83%.
2) The membrane surface modified by high purity alumina forms evenly distributed micropores, which can make lithium ions transfer efficiently between positive and negative poles.