β”-氧化铝固体电解质管的挤压制造工艺
Y. Hu, S.N. Heavens, J.S. Blackburn, S. Blackburn
对于未来的固定储能需求,钠电池由于其高能量密度、可靠可靠性、高法拉第效率和丰富的低成本原材料的使用,是潜在的合适人选。管状电池设计需要一个薄壁固体电解质管,通常由离子导电β " -氧化铝陶瓷形成。最先进的制造方法,即等静压和电泳沉积,贡献了电池成本的很大一部分,并且需要确定一种大批量低成本的陶瓷工艺。挤出为快速低成本、大批量生产工艺提供了潜力,但需要特殊的发展以适应固体电解质生产的要求。本文总结了挤压生产β″-氧化铝陶瓷电解质管的最新试验。
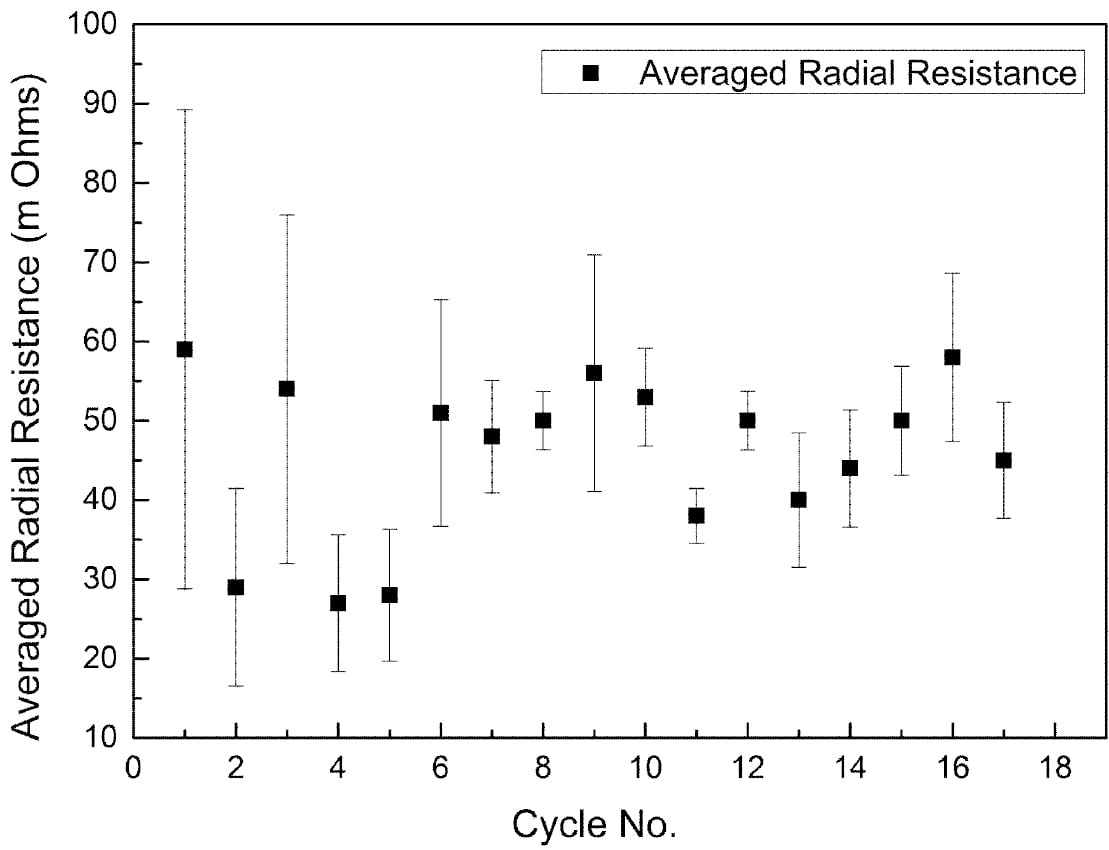
1. 介绍
高温钠电池具有高能量密度、零自放电率、100%的法拉第放电和充电效率、经过验证的长期可靠性以及丰富的低成本原材料1-2等优点,是未来大规模、高性价比的固定式储能需求的理想候选。固体电解质通常配置为管状薄壁陶瓷,由离子导电Na beta″-氧化铝形成,这是一种非化学计量铝酸钠,由Li或Mg 3的掺入稳定。这是电池性能的关键组成部分,需要优化微结构和相纯度,以确保良好的电气和机械性能。
生产β”-氧化铝固体电解质的最先进的制造方法包括等静压4和电泳沉积(EPD) 5。两者都是批处理工艺,需要大量的工艺步骤,大大增加电池成本。对于大批量生产,最好确定一种简化的低成本连续生产工艺。挤压提供了这种潜力,但需要特殊的发展,以适应固体电解质的生产,包括选择兼容的粘合剂,可挤压剪切稀化流变的捏合,以及具有所需几何形状的模具设计,包括形成封闭端管6-8的方法。
以前已经做了一些努力来挤压β″-氧化铝,但糊状配方很复杂9,多年来,似乎没有做出进一步开发该工艺的尝试。我们从相对简单的膏体配方(非水和水)开始,对β ” -氧化铝的挤出进行了全新的研究,目的是实现工艺步骤少的流线型工艺。本文将描述实现具有适当一致性和流变性的挤出膏体配方的挑战,并简要讨论其他重要问题,如模具设计,挤出后干燥和处理,以及烧结。以预转化beta″-氧化铝为原料的溶剂型工艺取得了良好的效果;理想的商业原料水工艺需要进一步的发展。
2. 实验的程序
(1)膏体制备
在高剪切真空z型叶片混合器(Werner & Pfleiderer混合器,ZD 224s)中加入粘结剂进行搅拌,形成均匀的可挤出膏体。捏合过程需要1 – 2小时的时间,以确保粘结剂在膏体中均匀混合。用毛细管挤出流变仪测定了膏体的流变特性。
考察了原料粉末的两种来源:
(A) β氧化铝钠/氧化锆粉末混合物,含有等量的β’-和β”-氧化铝相的混合物,其中添加了一定比例的氧化锆。
(B)制备了具有与β”氧化铝钠组成相对应的化学配方的市售原料粉末的前驱体混合物。起始粉末为72.7 wt%的氧化铝(a-Al2O3 <1.0µm), 17.3 wt%草酸钠和10.0 wt%碳酸锂。使用氧化锆球将粉末一起干燥1小时。
在下面的文本中,基于这些起始材料的工艺分别被称为方法A和方法B。对于这两种方法,β”-氧化铝稳定剂都是Li, ZrO2的比例按重量计为6%。在§II(4)中描述了包含ZrO2的基本原理。对于方法B, 6 wt%的氧化锆(Mel Chemicals 3Y)在戊醇中分别湿磨3小时至预定的粒度,然后加入其余粉末。
在膏体配方中使用了两套粘合剂/添加剂体系,一套是溶剂型的,另一套是水性的。总的来说,方法A在溶剂型膏体上更成功,而方法B在水性膏体上更成功;然而,所有的排列都被调查了。溶剂型膏体由77.8%粉末、7.8%聚乙烯丁醛、0.25 wt%硬脂酸、0.4 wt%亚麻油和13.75 wt%环己酮组成。水糊由85.5 wt%粉末,2.5 wt%羟丙基甲基纤维素,0.6 wt%硬脂酸和11.4%去离子水组成。
(2)管材挤压、干燥、烧结
传统的挤出机模具设计被发现不足以处理高挤压压力下的刚性膏体。伯明翰大学设计了一个特殊的模具,包含8个直径为9毫米的孔,如图1所示。
图1:开放式管挤压模具设计。
膏体采用Loomis 232 – 16-DT挤出机以20 mm/min的挤出速度挤出,形成直径为18 mm、壁厚为1 mm的开口绿管。
在挤压状态下,绿管是湿的,容易因重力和搬运而变形。挤出后处理和干燥系统,以支持湿管的重量和形状,以获得一个直无缺陷的干绿管是必要的。在一夜的干燥步骤中,绿色管以振荡运动滚动,以保持管的直线度,并消除管截面从圆形到椭圆形的扭曲。
在单次烧制循环中,管被封闭在镁坩埚中,以保持氧化钠蒸气压在1650°C的高烧结温度下持续15分钟。在烧结之前,通过在1000°C加热3小时来燃烧粘合剂。
(3)描述
采用x射线衍射、扫描电镜(SEM)和能谱分析(Philips XL-30 FEG环境扫描电镜(Environmental SEM)和牛津印加能谱仪(Oxford Inca EDS)对烧结形态的相纯度和微观结构进行了分析。孔隙度是通过阿基米德技术测量密度来确定的。轴向离子电导率(沿管的长度)在温度范围25 – 600°C使用铂电极交流4端方法测量。
在Na/β”-氧化铝/NaNO2测试槽中测量径向离子电导率(穿过管壁),其电化学活性部分如图2所示。一个beta″-氧化铝管的长度60毫米是通过玻璃连接在底部到一个氧化铝盘和在顶部到一个300毫米长的氧化铝管关闭。一根铝管形成了中央钠阳极集流器,用硅橡胶与氧化铝管密封,并连接到真空系统,这样内部(钠)隔间就可以被抽走并回充氮气。β ” -氧化铝管完全浸没在熔融的NaNO2中。通过beta″-氧化铝管的电压测量之间的镍线包裹管和铝电流收集器。径向传导单元更具代表性比条件下的轴向测量中遇到钠电池应用程序,但更容易变化是由于界面电阻焊不良所产生的并发症,杂质和其他因素。
图2:用于测量径向电导率的β ” -氧化铝管组件。
(4)氧化锆掺入β″-氧化铝
为了本研究的目的,引入ZrO2到陶瓷中形成复合材料的主要目的是ZrO2是一种有效的烧结助剂,这是由锆酸钠共晶的可能形成引起的,从而促进液相烧结。这在方法B的情况下尤其有益,该方法需要反应烧结过程,其接近理论密度的实现被证明比方法a更具挑战性。
此外,使用ZrO2/β”-氧化铝复合材料作为固体电解质还有其他原因。β″-氧化铝陶瓷中的杂质,特别是钙,会导致电化学电池中的电阻严重退化,ZrO2是Ca的有效清除剂。在合理低水平的添加(<10%重量),ZrO2可以导致电阻率轻微降低,而不是预期的增加,因为在大多数感兴趣的电池温度(~ 300°C) ZrO2是绝缘体。此外,ZrO2相的存在防止了烧结过程中不受控制的二次晶粒生长,从而提高了机械强度、威布尔因子和韧性。复合陶瓷固体电解质在NaS电化学电池中表现出优异的耐久性和低故障率。
无论采用何种成型工艺来获得绿色形状,ZrO2相都必须很好地分散在β”-氧化铝基体中。为了实现ZrO2颗粒的精细分散,方法b需要单独的湿磨工艺。粒径和SEM分析表明,ZrO2粒径与粒径控制之间有很强的相关性。未磨碎的ZrO2(图3a)显示了一些高达100 lm的大颗粒,并且在烧结陶瓷中观察到夸张的晶粒生长。通过研磨ZrO2(图3b),获得了更均匀的粒径,烧结陶瓷中的晶粒尺寸限制在最大10 lm。
图3:扫描电镜(a)未研磨(b)研磨后的氧化锆粒径分布及相应的烧结陶瓷微观结构。
3. 结果与讨论
(1)视觉质量和维度方面
图4 (a)和(b)分别为方法a和方法b的烧结管。对于A方法,获得了长度达300mm或以上的优质直管。方法B在获得良好的可挤压浆料质量方面存在更大的困难,所得到的烧结管在直线度和截面上表现出更大的偏差,这表明需要进一步优化工艺。
(2)陶瓷相纯度
A和B两种方法的挤压和烧结样品均有较高的比例(>98 %) β”-氧化铝相为β/β”相,作为高Na+导电性的要求。
(3)陶瓷密度
方法A所得陶瓷的理论密度为98.6%,方法B所得陶瓷的理论密度为96.3%。方法B的低密度可能与未转化原料粉末的反应烧结需求有关,而方法A的起始粉末已经预先转化为β / β”-氧化铝。
图4:用(a)方法a和(b)方法b得到的烧结管。
(4)离子电导率
用A方法获得的挤压β″-氧化铝/ZrO2管在20 – 500℃范围内具有可重复的轴向电阻率(表1和图5)。在300℃时,电阻率为4.37±0.70 X⋅cm,与Ionotec基于EPD 11的生产工艺生产的相同组成的管的平均值4.46±0.63 X⋅cm相当。
表1:烧结b″-氧化铝管的轴向电阻率。
自由基电导电池(§II(3),图2)成功运行了18个完整的充放电周期,但电阻测量更分散(图6)。在循环9时,电池在1.17 a速率下的充放电容量分别为3.82 Ah和3.17 Ah(图7)。累积容量分别为+ 41.75 Ah和- 37.63 Ah。从循环过程中观察到的最小电阻数据来看,在300℃时陶瓷电阻率为5.7 ×⋅cm。对于用EPD生产的管,同样的测量技术得到4.7 X⋅cm,接近轴向电阻率的结果。挤压管的较高径向电阻率可能代表陶瓷微结构的纹理程度(优选的晶体取向),或者在300°C时陶瓷和液态钠之间润湿行为的可变性。
图5:挤压β”-氧化铝管的轴向电阻率。
图6:挤压β”-氧化铝管在18个循环中的平均径向阻力。
图7:Na/β”-氧化铝/NaNO2电池的轴向电阻和容量,周期9。
4. 总结与结论
直薄壁ZrO2/β”氧化铝管可以通过挤压生产,具有可接受的陶瓷质量,用于电化学电池的固体电解质。由预转换β/β”-氧化铝/ZrO2粉末生产的管显示出与EPD工艺生产的性能相似。由未反应前体粉末生产的前体粉末需要进一步的工艺开发,以达到预转化粉末所达到的标准,尽管后一种工艺在显著降低制造成本方面具有更大的潜力。